The Problem
One of the challenges transportation organizations face is maintaining roads through concrete repair. Delayed drivers get irritated, and extended closures on interstates can have regional business impacts. Safety is another aspect for consideration as prolonged repair times increase worker exposure to motor-vehicle accidents. However, if lanes are re-opened too quickly there is the potential that low-strength concrete may be unsafe for traffic. The solution is fast patch mixes.
A fast patch mix is concrete designed to set and gain strength quickly to speed up the concrete repair process. A typical fast patch mix may be ready for traffic within a 5-hour window. These mixes rely heavily on high cement content and calcium chloride to achieve set and strength goals. However, this combination can be extremely challenging to work with. Current fast patch mixes may only allow 30 minutes after batching before the concrete becomes unworkable. These mixes have also historically had reduced long-term durability, which means more frequent roadway closures for repair and replacement.
Designing a Solution
Premiere Concrete Admixtures LLC., is heavily involved in research and development to support local and state departments of transportation. Recently, Premiere demonstrated a new fast patch mix design. The design is appealing to departments of transportation for a few major reasons, the first being workability. Premiere’s fast patch more than doubled workable time without sacrificing rate of set. In other words, the concrete remained workable for over an hour but still gained its desired strength within the 5-hour target window.
The second benefit of Premiere’s mix design is increased long-term durability. This was achieved in part thanks to the addition of a specialty product of Premiere’s called Impede® IntraSeal. IntraSeal creates a water repelling barrier throughout concrete, and is known for reducing the effects of freeze-thaw damage and brine penetration. This is an essential component to durability in concrete that is treated during winter months with deicing chemicals. Impede® IntraSeal has been used in municipal roadways to increase durability, but fast patch is a new application of the technology.
In addition to traditional flexural and compressive strength testing, Premiere had a unique way of demonstrating the strength of their mix. Five hours after the concrete was batched, a fully loaded 40-ton Premiere semi-tanker barreled toward the fresh patch of concrete. It drove over the patch, stopped, and then backed over the patch again, coming to a stop on top of it. An examination of the surface confirmed what lab testing had already concluded. The patch was unmarked due to sufficient flexural strength gain within the specified 5-hour curing window.
Leveraging Technology
Concrete test specimens were match cured in Con-Cure LLC’s TruMatch™curing box. Utilizing NEX® concrete temperature monitoring, TruMatch™ allowed Premiere to cure test specimens at exactly the same temperatures as the fast patch concrete in the field. Since time and temperature are the variables that account for concrete maturity and strength gain, specimen break results could be trusted as an accurate indicator of field concrete strength.
Premiere utilizes cutting-edge technology like TruMatch™, NEX®, and Impede® IntraSeal to redefine standards for the concrete industry. The new fast patch gives departments of transportation a mix that is easier to work with and more durable, while meeting acceptable strength gain and rate of set specifications. For more information or product related inquiries please contact us here!
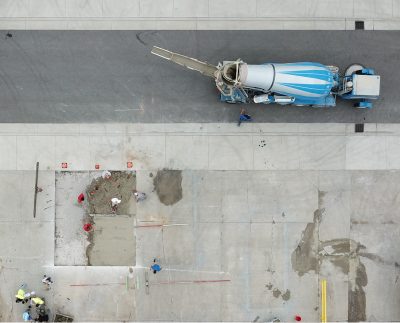
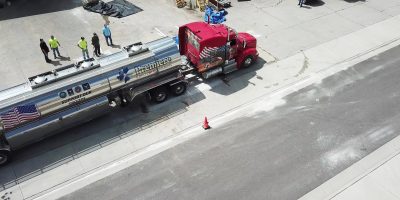